

The problem necessarily results from factors known as the 5Ms: Materials, Machines, Methods, Manpower, Medium. The “5 whys” method, which aims to ask the question “why” until you get to the root cause of the problem.Īnother option is the Ishikawa (or Fishbone) method and its causes and effects diagram. The detective work begins! It’s time to investigate the root causes of the problem, the true reasons why the goal was not met. By following this principle, you will be sure to set your goals properly, so that they are understood and achievable by all. Think SMART! This acronym refers to the 5 adjectives that qualify your goals: Specific, Measurable, Achievable, Relevant, Time bound. This provides you with a great overview of the situation, helping you to fully understand the problem. By listing all the actions involved in the process, you highlight those with high added value, and those with low added value. Nothing better than a Value Stream Map (VSM) to easily view the production chain, from the supplier to the customer. You naturally shed the light on the end goal, to make sure that the problem will not happen again in future. Analyzing these 5 elements highlights the ins and outs of a process, and helps determine the core of the problem and its consequences. The acronym SIPOC stands for Suppliers, Inputs, Process, Outputs, and Customers. Start by using the SIPOC method, ideal for a detailed description of a process. Stage 1: Describe the problem and set the end goal. This phase involves preparing the work, from the factual description of the problem, up to the tasks to be done, as well as setting goals. This cycle encompasses 8 phases, which must be completed as a team, and repeated until the end goal is met. Check that the retained solution is in line with the expected outcome Understand the problem and find its root cause It is a clear reference point for the team, for each new project.Ĭommonly used as a problem-solving tool, the A3 report can also have other uses, such as making suggestions and demonstrating their relevance.ĭesigned according to a PDCA cycle (a.k.a Deming wheel), the A3 report follows a specific protocol, that aims to: It’s a highly visual tool, with a standardized framework that promotes analytical and synthetic skills, where everyone focuses on key elements. They are part of the Deming wheel, with a 4-phase cycle that is part of a continuous improvement approach: Plan-Do-Check-Act (PDCA).Īn A3 report is a team process, not an individual one. The A3 report covers a sequence of 8 successive stages.
#A3 project management template how to
But it means you have to be to the point, know how to prioritize and be concise.
#A3 project management template trial
A3 management is a system based on building structured opportunities for people to learn in the manner that comes most naturally to them: through experience, by learning from mistakes and through plan-based trial and error.A 42 x 29.7 cm sheet of paper is not that big when it comes to reporting, analyzing and solving a problem.
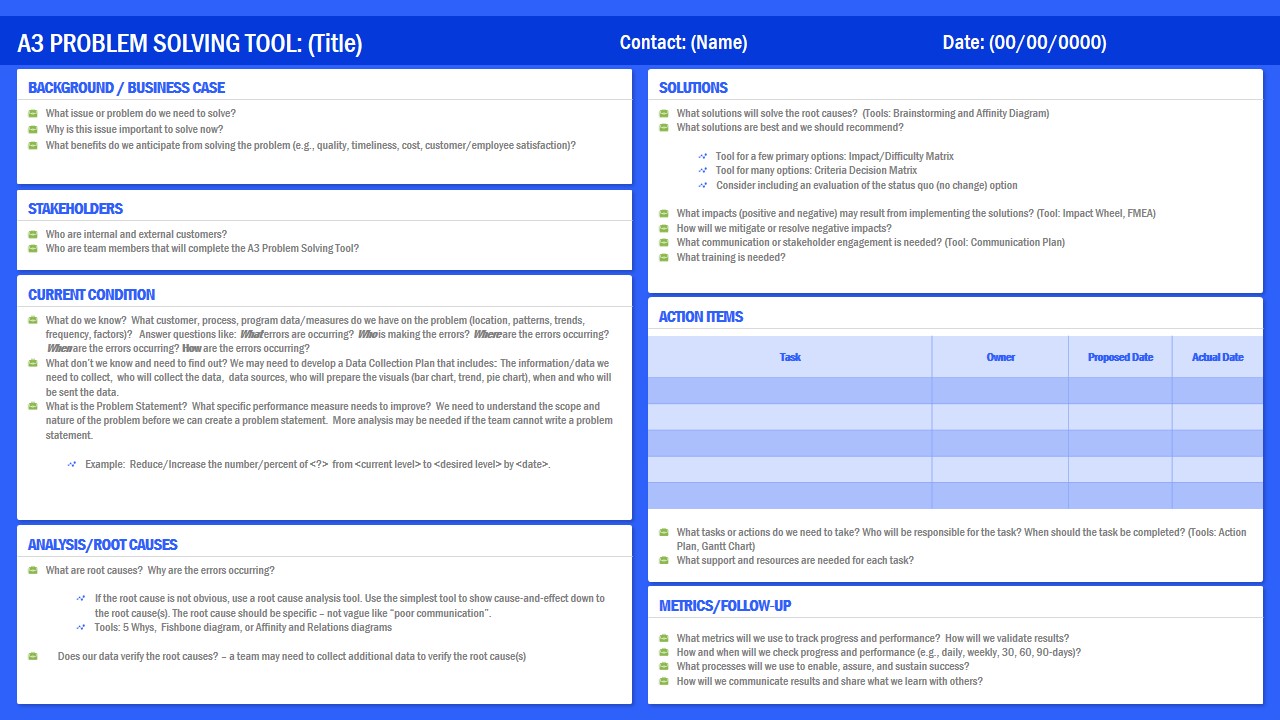
A3s serve as mechanisms for managers to mentor others in root-cause analysis and scientific thinking, while also aligning the interests of individuals and departments throughout the organization by encouraging productive dialogue and helping people learn from one another. However, A3 reports - and more importantly the underlying thinking - play more than a purely practical role they also embody a more critical core strength of a lean company.
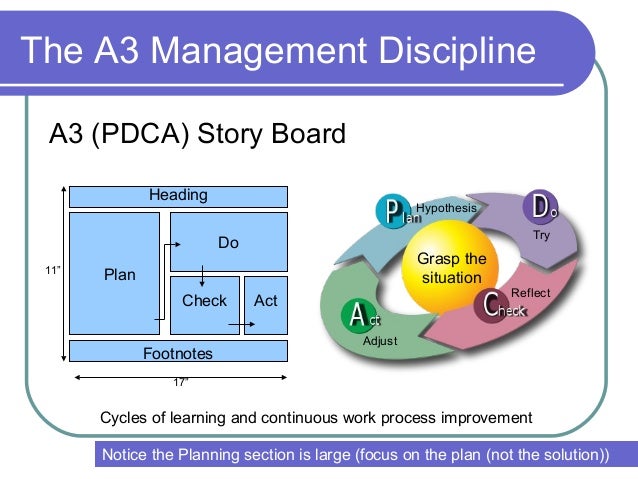
It presents ideal opportunities for mentoring. Though the A3 process can be used effectively both to solve problems and to plan initiatives, its greatest payoff may be how it fosters learning.The A3’s constraints (just 2 pages) and its structure (specific categories, ordered in steps, adding up to a “story”) are the keys to the A3’s power.Toyota has designed a two-page mechanism for attacking problems. Inside the boxes the A3’s “author” attempts, in the following order, to: (1) establish the business context and importance of a specific problem or issue (2) describe the current conditions of the problem (3) identify the desired outcome (4) analyze the situation to establish causality (5) propose countermeasures (6) prescribe an action plan for getting it done and (7) map out the follow-up process. An A3 is composed of a sequence of boxes (seven in the example) arrayed in a template. Company managers use a tool called the A3 (named after the international paper size on which it fits) as a key tactic in sharing a deeper method of thinking that lies at the heart of Toyota’s sustained success.Ī3s are deceptively simple. At Toyota, there exists a way to solve problems that generates knowledge and helps people doing the work learn how to learn. While much has been written about Toyota Motor Corp.’s production system, little has captured the way the company manages people to achieve operational learning.
